PRODUCT INFORMATION TOO TECHNICAL?Visit Lysaght.com
11 / November / 2015

Ipswich, Queensland
BUILDER
Leda Developments Pty Ltd
FABRICATOR
Formbrace Pty Ltd
Alltype Welding
Products
LYSAGHT BONDEK® structural steel formwork is playing a key role in the construction of South East Queensland's newest shopping centre. Formwork companies, Formbrace Pty Ltd and Alltype Welding, have been selected by Leda Developments Pty Ltd to provide formwork for the major slab structures.
The Riverlink Shopping Centre will provide a new retail focus for an area which has previously lost out to surrounding centres.
At 57,000 square metres, the Leda Developments project will be almost identical in size to the original Logan Hyperdome, which was also built by Leda. Riverlink will provide premises for 130 tenants including Coles, Bi-Lo, Kmart, Target, bulky goods retailers and brand direct outlets.
There will also be car parking for 2,000 vehicles. Travelators will move shoppers to and from the centre.
The Ipswich Riverlink site is located at the northern edge of the Ipswich central business district, less than an hour's drive west of Brisbane. The new centre will feature an elevated food court overlooking the Bremer River.
Formbrace Pty Ltd
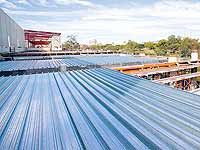
Formbrace Pty Ltd was selected by Gold Coast based Leda Developments Pty Ltd to provide formwork for a major slab structure at Leda's newest retail development, the Riverlink Shopping Centre at Ipswich, west of Brisbane.
LYSAGHT BONDEK®, previously chosen as structural steel formwork for the carpark precinct of the major new shopping complex is an integral part of the construction of South East Queensland's newest shopping centre.
"We are involved in the western precinct which houses the retail premises," Formbrace Project Manager Renee Tan said. "It is the major part of the development and has been designed specifically for post tensioned concrete. We are dealing with 30,000 square metres of suspended slab which is a very large area. Certainly it is one of Formbrace's largest projects in Queensland. Because of that we are making every effort to ensure that the result is one with which the developer, the tenants and we are completely satisfied."
Formbrace, which has major offices in Sydney and Brisbane, has a formidable reputation to protect.
Over nearly 20 years it has completed a succession of large commercial and retail projects in Sydney and, more recently, Brisbane.
It is also working on the Portside Wharf development at Hamilton in Brisbane, a Multiplex project, which will give Brisbane its first major terminal for cruise lines.
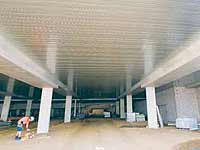
"We are also involved in residential projects at Southport on the Gold Coast," Renee Tan said. "With all this activity it is important that we use only the best formwork systems for each project. By that I mean systems which deliver the best quality results in the minimum amount of time and are also cost effective. On a project such as Riverlink we need to get in and do our work so that the following trades can get on with their jobs and keep the building program on schedule."
"This is a big plate project with all the retail activities taking place on one level over 30,000 square metres. With that kind of layout you can't afford to have any delays. You need a formwork system which makes it easy to cover large areas day after day."
Renee Tan pointed out that at any one time three stages of the formwork activity are underway at different parts of the slab.
"In some areas we are laying the LYSAGHT BONDEK®, in others the concrete is being poured and in yet other areas of the site we are stripping out to provide access for following trades," he said.
"Utilisation of 0.75mm LYSAGHT BONDEK® allows faster cycle times between installing formwork, pouring concrete to stripping props and supports and then being able to set up the next formwork stage.
"This leads to overall improvement in cost effectiveness of the formwork system and allows an accelerated construction schedule, hence providing a win/win situation for developer and formworker. That requires co-ordination and total confidence in your supplier, in this case BlueScope Lysaght. The work requires 30,000 square metres of 0.75mm BONDEK® and we have had great support from BlueScope Lysaght to stage the deliveries so that the laying of the formwork for the slab can proceed smoothly."
"The 0.75mm BONDEK® arrives on site cut to length, so that waste is kept to a minimum. Our workers are experienced with BONDEK®, which is an advantage, but it is the type of structural steel formwork system that anyone can install, even with minimal experience."
Alltype Welding
Experienced contractor Alltype Welding is using 18,000 square metres of LYSAGHT BONDEK® as structural steel formwork for slabs in the carpark levels of the Riverlink project.
Alltype recently completed work on a shopping centre redevelopment project at Morayfield, also a Leda Developments project.
"We started out as steel fabricators, but builders are increasingly looking for contractors who can do more than just one role," Peter Jakubenko of Alltype Welding said.
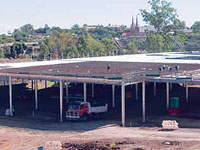
"We had our first experience installing structural steel decking from BlueScope Lysaght at Morayfield and that gave us the confidence to offer the combination of steel fabrication and the supply and installation of structural steel formwork again for Riverlink.
"Our workers have very quickly got up to speed working with LYSAGHT BONDEK® even though they have had no previous experience with it.
"For slab above ground work it is hard to beat, especially when the layout has large areas where you just lay out the sheets and keep moving."
Peter Jakubenko estimated that even his inexperienced crew could lay out and secure the structural steel decking for which he had contracted at Riverlink in just six weeks.
"The system works well and we have had good support from BlueScope Lysaght," he said. "Order scheduling hasn't been a problem. We just call BlueScope Lysaght and they deliver enough product so that we can get on with our work without cluttering up the building site. We are using 1.0mm BONDEK® and it arrives on site cut to size, so we just crane it up to the work level on the steel frame. The sheets are 8.7 metre lengths and our guys are using static lines to walk it out."
With the experience of a career working with steel, Peter Jakubenko has a clear preference for BONDEK® over traditional formwork.
"People raise the issue of weight, but that is in fact a positive for steel," he said. "If you were laying out traditional formwork over the same 18,000 square metres that we are, then each worker would be lifting far more material into position than they are with BONDEK®. You just have to recognise the other advantages such as speed and cost and apply them to jobs on which you are quoting."
"Alltype Welding's experience with structural steel formwork has been that it is a simple solution which can be installed without having to rely on highly skilled labour which can be difficult to find. In our case it has allowed us to expand our offering to builders so that we fabricate and stand the steel frame and then supply, lay out and secure the steel formwork for large slabs which will support car parking and retail areas."
"By contracting us to do that work and to use BONDEK® structural steel formwork, the builder has saved money and also reduced the number of contractors on site, which simplifies his coordination role for the whole project."
LYSAGHT BONDEK® decking is the original steel formwork system that revolutionised concrete construction. It is made from DECKFORM® zinc coated high tensile steel which was developed by BlueScope Steel specifically for the steel decking market. It delivers excellent durability and is backed by a BlueScope Steel warranty and nationwide technical support.
Steel formwork requires less propping than traditional ply formwork, and there is no stripping, which reduces material handling on site, leading to faster installation and reduced cycle times.
Ipswich, Queensland
BUILDER
Leda Developments Pty Ltd
FABRICATOR
Formbrace Pty Ltd
Alltype Welding
Products